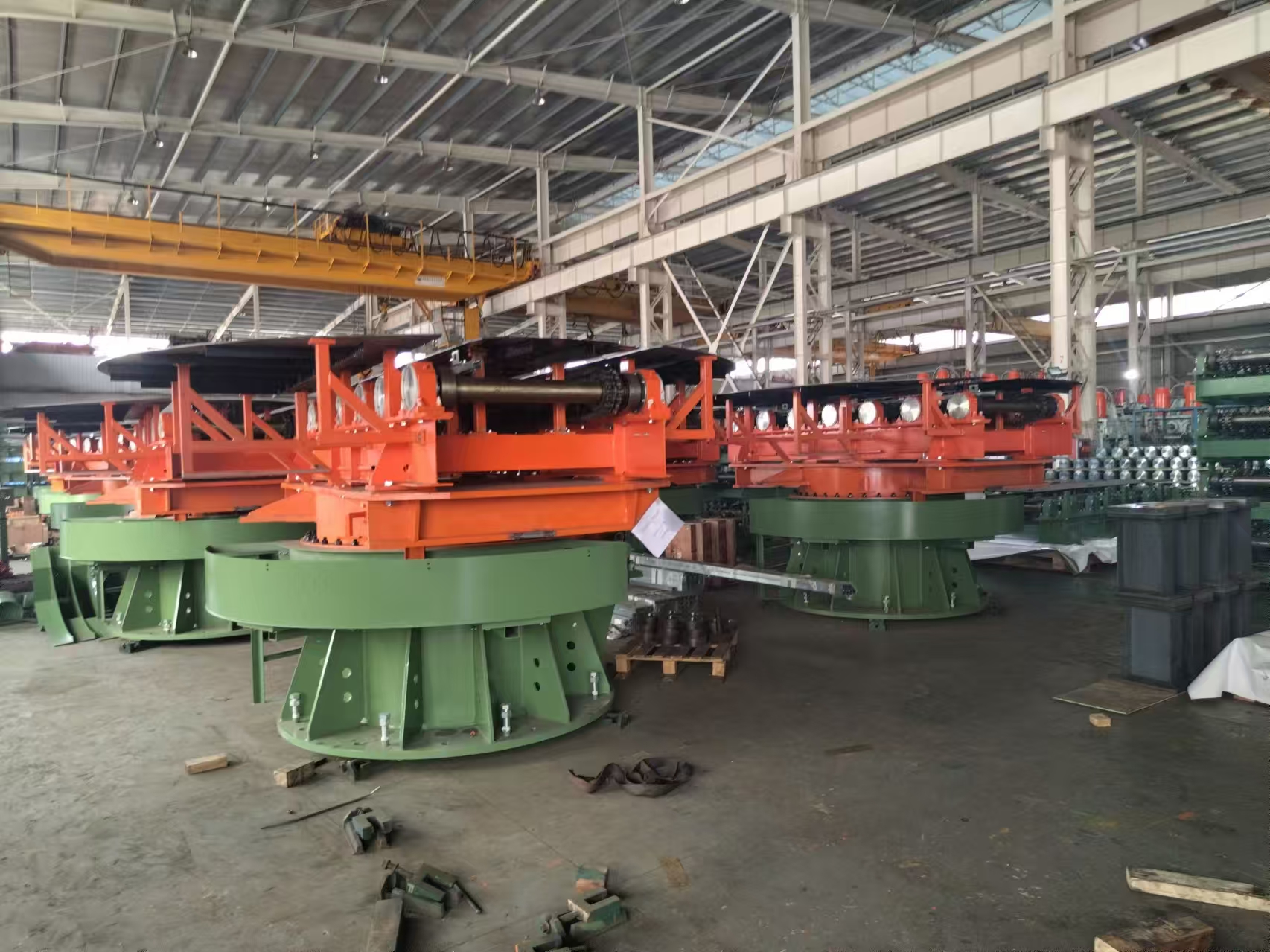
High-Performance Submerged Entry Nozzle for
Continuous Casting Excellence
Product Category
Our Submerged Entry Nozzles are categorized into several types to meet diverse industrial requirements.
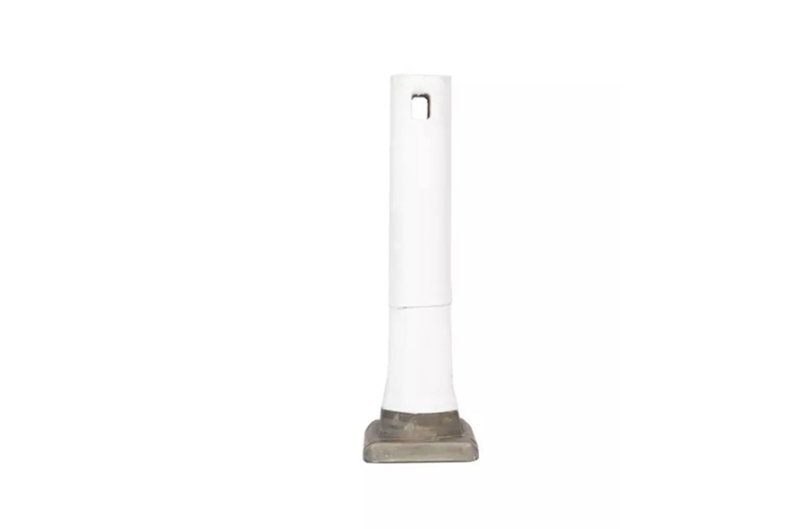
Standard - Type Submerged Entry Nozzles:
These are designed for general - purpose applications in steelmaking. They offer a reliable and cost - effective solution, ensuring smooth molten steel flow into the mold with consistent performance.
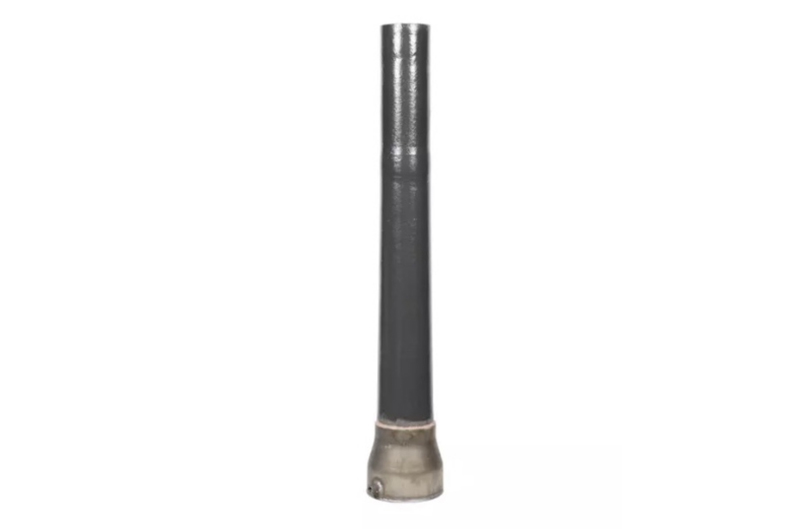
Special - Design Submerged Entry Nozzles:
Tailored for specific steel grades and casting conditions, these nozzles feature unique geometries and material compositions. For example, when casting high - alloy steels that demand precise control over the flow and temperature of the molten metal, our special - design nozzles are engineered to optimize the casting process.
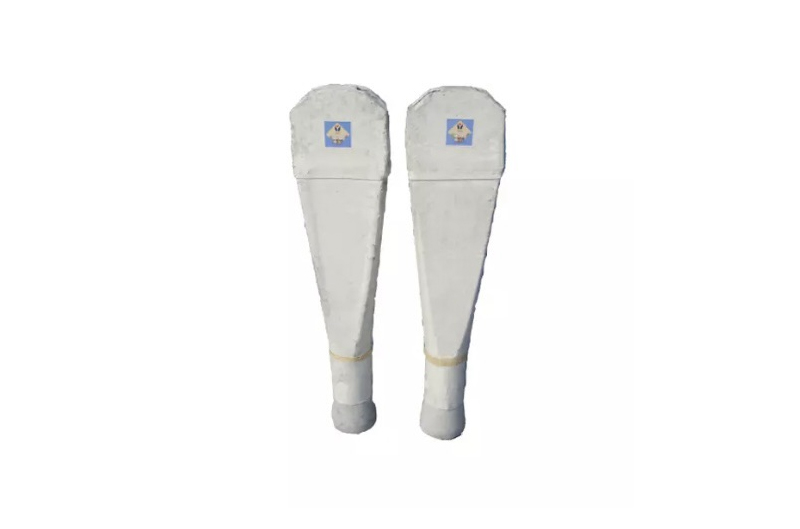
Customized Submerged Entry Nozzles:
Understanding that each customer may have unique production needs, we provide customized solutions. From adjusting the size and shape of the nozzle to incorporating specific functional features, we work closely with clients to develop nozzles that perfectly fit their steel - casting operations.
Application
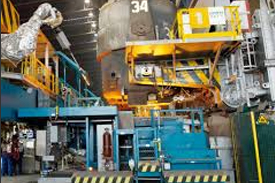
Steel Mills:
In large - scale steel - making facilities, our nozzles are used to direct the molten steel from the tundish into the mold. They ensure a stable and controlled flow of the molten metal, which is essential for producing high - quality steel slabs, blooms, and billets. This helps in reducing surface defects and improving the internal structure of the cast products.
Alloy Production:
When manufacturing various steel alloys, the Submerged Entry Nozzle helps in maintaining the integrity of the alloy composition during the casting process. By precisely controlling the flow of the molten alloy, it enables the production of alloys with consistent chemical properties and mechanical performance.

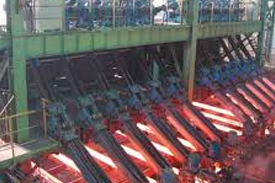
Specialty Steel Manufacturing:
For the production of specialty steels such as stainless steel, electrical steel, and high - strength low - alloy steel, our nozzles are designed to meet the stringent requirements of these materials. They contribute to achieving the desired surface finish and internal quality of the specialty steel products, making them suitable for applications in industries like automotive, construction, and electronics.
Product Advantages
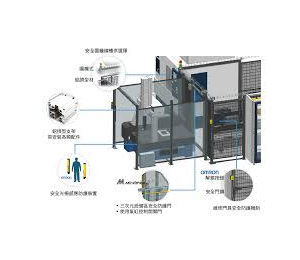
Frequently Asked Questions About Submerged Entry Nozzle
What is a Submerged Entry Nozzle (SEN), and why is it critical in continuous casting?
A Submerged Entry Nozzle is a refractory component that delivers molten steel from the tundish into the mould in continuous casting. By remaining submerged below the metal bath surface, it minimizes slag entrainment and promotes a stable, controlled flow. Proper SEN design and material selection are vital to achieving uniform solidification, reducing inclusion defects, and improving overall yield.
Which materials and grades of refractory are used for manufacturing high-performance SENs?
SENs are typically made from alumina-magnesia, alumina-silica, or high-purity alumina refractories. Choice of grade depends on thermal shock resistance (to withstand rapid temperature changes), erosion/corrosion resistance (to resist chemical attack by slag and liquid steel), and strength at temperature (to maintain dimensional stability under load). Advanced composite formulations—such as graphite-impregnated or nano-engineered refractories—can further extend service life and reduce clogging.
How do I select the optimal SEN geometry for my casting parameters?
Key factors include mould width and casting speed (which determine the cross-sectional area and wall thickness of the nozzle port), superheat and steel grade (which influence flow rate and erosion potential), and desired flow pattern (single-, double-, or multi-port nozzles shape the jet to control turbulence and inclusion flotation). Consult with your refractory supplier’s metallurgical engineers to model the flow using computational fluid dynamics and choose an SEN whose port design matches your specific casting recipe.
What are the most common failure modes of SENs, and how can they be mitigated?
"Clogging, caused by solidified steel or slag freezing at the ports—mitigate by optimizing tundish chemistry and maintaining adequate superheat.
Erosion, accelerated by high-velocity jets—use higher-alumina or composite refractories in high-wear zones.
Thermal shock cracking, from rapid temperature changes—implement controlled copper backup cooling and pre-heating procedures.
Chemical corrosion, due to aggressive slag components—apply protective coatings (e.g., SiC or CVD layers) to the interior bore."
How should SENs be stored and handled on-site to preserve their integrity?
They should be kept in a dry, well-ventilated area with relative humidity below 60 percent to avoid moisture uptake. Store horizontally on supports that run the length of the nozzle to prevent point stresses or warping. Use protective covers to shield port openings from dust and accidental damage. Rotate inventory on a first-in, first-out basis to ensure refractories are used before shelf-aging effects set in.
What maintenance and inspection routines are recommended to maximize SEN service life?
At each heat change, visually inspect port openings for signs of clogging or rounding. Measure port diameters against original specifications—a reduction in clearance greater than 10 percent often indicates replacement. Replace nozzles when erosion has reduced wall thickness below the manufacturer’s minimum or when multiple cracks are visible. Log each nozzle’s campaign life, steel grades cast, and any abnormal events to refine future selection and maintenance schedules.
How does SEN cost compare to its impact on steel quality and yield?
Premium-grade or composite-coated SENs cost 10 to 30 percent more than standard refractories but deliver fewer inclusions, reduced breakout risk, and longer campaign life. When weighed against the high cost of an unscheduled stoppage or unacceptable slab quality, investing in optimized SEN technology produces substantial savings and productivity gains over the furnace campaign.
Let's Connect
Our industrial raw materials are at the forefront of innovation in the industry. We have developed unique product formulations and processing methods. If you are interested in our Creatine Monohydrate products, please fill out the form below. We will contact you to initiate the first step of cooperation and boost your business development.
Phone:+86-15993156766
Email:harryjin@ghongsteel.com
Live Chat:Available on our website